伴热带支持与其他加热设备联动控制,且可通过多层级协议、硬件接口及智能策略实现协同运行,满足复杂工业场景的精准控温需求。以下从技术可行性、联动模式、实施要点及典型案例展开分析:
一、技术可行性:多维度联动支撑体系
通信协议兼容性
硬件接口标准化
智能算法集成
二、典型联动模式与场景
主从式联动
主设备:锅炉蒸汽加热系统(维持管道入口温度60℃)。
从设备:伴热带(覆盖易散热段,如高架管段)。
联动规则:当蒸汽压力下降导致入口温度<55℃时,伴热带自动启动;当入口温度恢复至58℃时,伴热带降功率至30%运行。
应用场景:原油长输管道伴热。
控制逻辑:
效果:能耗降低35%,避免蒸汽加热盲区导致的介质凝固风险。
分层式联动
底层:伴热带(硅橡胶材质)预加热炉体至150℃(防止炉体冷热冲击开裂)。
中层:电阻丝加热器快速升温至600℃(实现材料晶型转变)。
顶层:红外辐射加热器(碳化硅管)精确控温至900℃(保证材料一致性)。
联动规则:伴热带在炉温<100℃时持续运行,100-150℃时功率线性衰减,>150℃时关闭。
应用场景:锂电池正极材料烧结炉。
控制逻辑:
效果:烧结合格率提升至99.2%,炉体寿命延长2倍。
应急联动
正常模式:伴热带(额定功率50W/m)维持卸料臂温度-30℃。
应急模式:当环境温度骤降至-40℃且伴热带功率达到上限时,触发以下动作:
应用场景:北方LNG接收站卸料臂伴热。
控制逻辑:
效果:LNG卸料中断时间从4小时缩短至15分钟,避免价值千万的滞期费损失。
启动电加热带(额定功率120W/m)作为补充热源。
关闭卸料臂非关键阀门,集中热量保障核心管段。
发送报警至中控室,提醒操作员启动柴油循环加热系统。
三、实施要点与避坑指南
电气隔离与抗干扰
采用光纤隔离器传输Modbus信号,隔离电压≥2500V。
伴热带电源线与控制线分开穿管,间距≥30cm。
在变频器输出端加装EMI滤波器,衰减率≥40dB。
问题:伴热带变频器与PLC的PWM信号相互干扰,导致温控器误动作。
解决方案:
安全冗余设计
一级:伴热带内置PTC限温器(动作温度135℃)。
二级:温控器超温报警(140℃切断电源)。
三级:SCADA系统远程急停(145℃触发全厂ESD)。
双电源冗余:伴热带供电系统采用ATS自动切换开关,主电源(市电)与备用电源(柴油发电机)切换时间<0.15秒。
三重温控保护:
数据融合与AI优化
四、成本效益与适用性分析
短期成本
长期效益
适用性边界
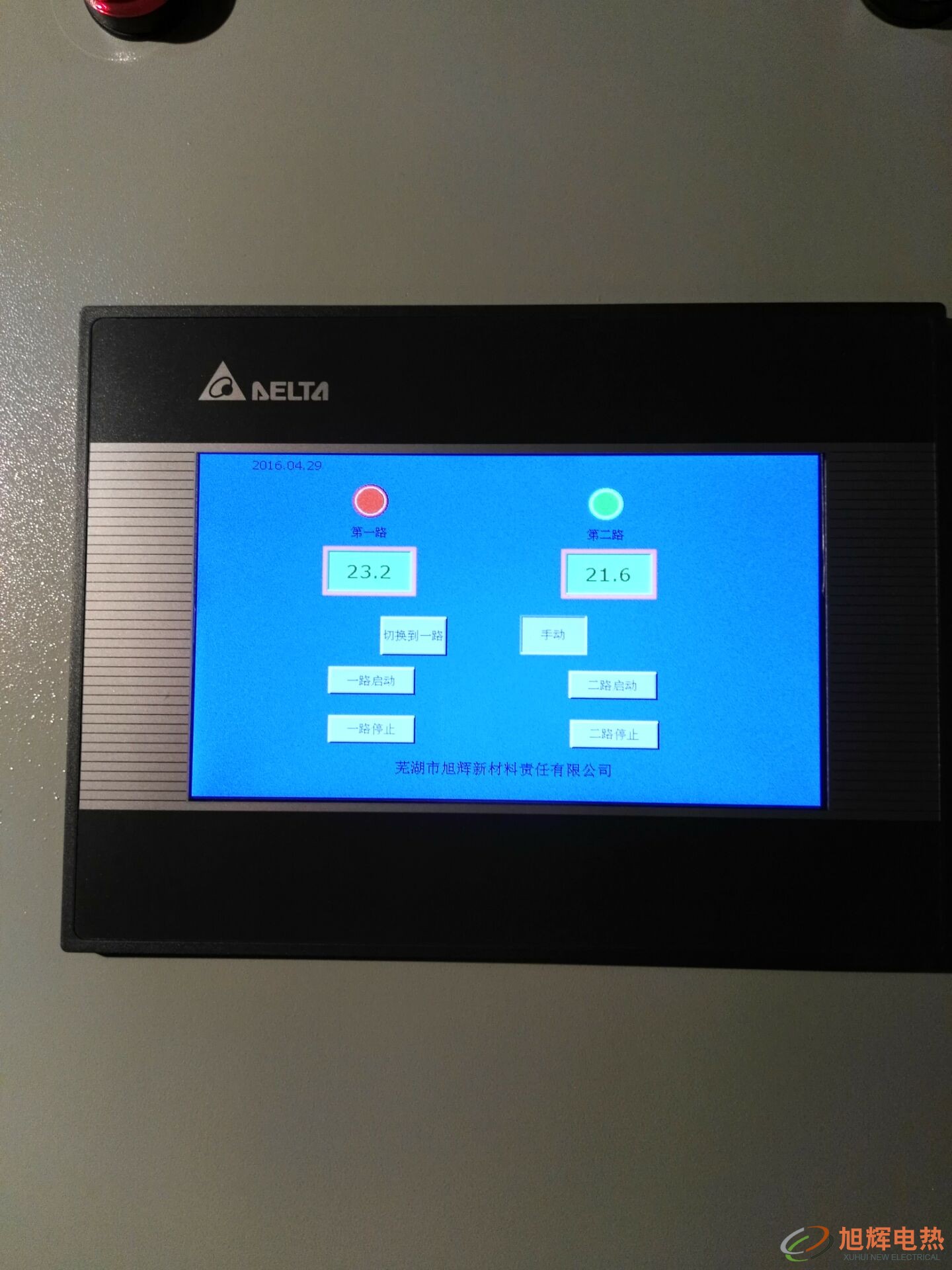